
Control humidity, decrease electrostatic discharges, and maintain uniform quality
In all electronics manufacturing facilities, reducing the risk of electrostatic discharges (ESD) is essential to avoid damage to sensitive components and to production equipment – not to mention the personnel working in the production facility. This is easily done by controlling air humidity. Here’s how:
Electrostatic discharges (ESD) typically occur when air humidity drops below a certain critical value.
Controlling air humidity will successfully minimize the risk of ESD, protecting both equipment and personnel and ultimately increasing productivity and preserving a consistent quality of the output. Optimal control of the air humidity is best achieved by installing an adiabatic air humidifying system.
How an air humidifying system helps in electronics production
Once air humidity is maintained above the recommended level, the humidity will ensure that static charges are kept at a minimum. Another benefit of an air humidifying system is its ability to utilize the adiabatic cooling effect to reduce excess heat generated locally by production processes.
In most cases, electronics producers must be able to document that their production takes place under strict control of indoor climate - and this is where air humidifying technology plays a key role.

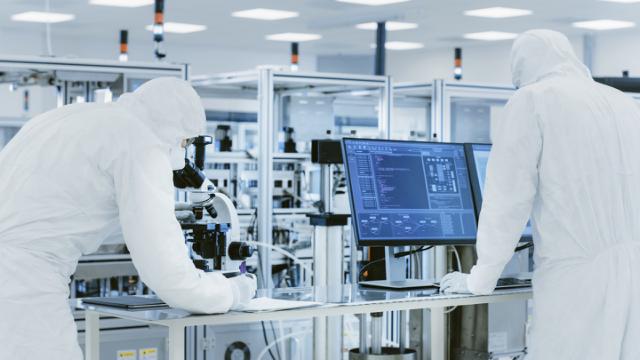
The benefits of air humidifying solutions in electronic production:
- Documentation of compliance with regulations concerning production environment
- Reduce risk of ESD, protecting personnel and products
- Adiabatic cooling
The benefits of a site assessment
Securing the optimum relative air humidity relies on an on-site assessment of the facility in question.
In close collaboration with the customer, Airtec’s project engineers will determine the requirements for the products and the facility such as seasonal variations, the presence of ventilation systems, the overall production layout, local sources of excess heat and many other parameters.
Such a site assessment allows us to provide recommendations about the optimum way of securing a productive environment with ideal air humidity. You can read more about our site assessment here.
An example: walking across a carpet can yield a charge of 35kV in dry air at 10% RH but will drop significantly to 7.5kV at 55% RH. In an electronics manufacturing environment lower humidity may result in lower output from production due to an increase in ESD events during manufacturing processes.

ACTIVITY (@ 21° C) | STATIC VOLTAGES | |
20% RH | 80% RH | |
Walking across vinyl floor | 12 kV | 250 V |
Walking across synthectic carpet | 35 kV | 1.5 kV |
Arising from foam cushion | 18 kV | 1.5 kV |
Picking up polyethylene bag | 20 kV | 600 V |
Sliding styrene box on carpet | 18 kv | 1.5 kV |
Removing Mylar tape from PC board | 12 kV | 1.5 kV |
Shrinkable film on PC board | 16 kV | 3 kV |
Triggering vacuum solder remover | 8 kV | 1 kV |
Aerosol circuit freeze spray | 15 kV | 5 kV |
The normal range for humidity in an electronics manufacturing environment is between 30% RH and 70% RH.
Some facilities try to maintain a constant moderate RH (~50%), while others may want a lower % RH due to humidity sensitive parts.
Thus, the ideal humidity level varies depending on the ambient environment and is usually determined by the specifications of the devices and components being assembled.